- Published at
Preparing for FDA Traceability Inspections
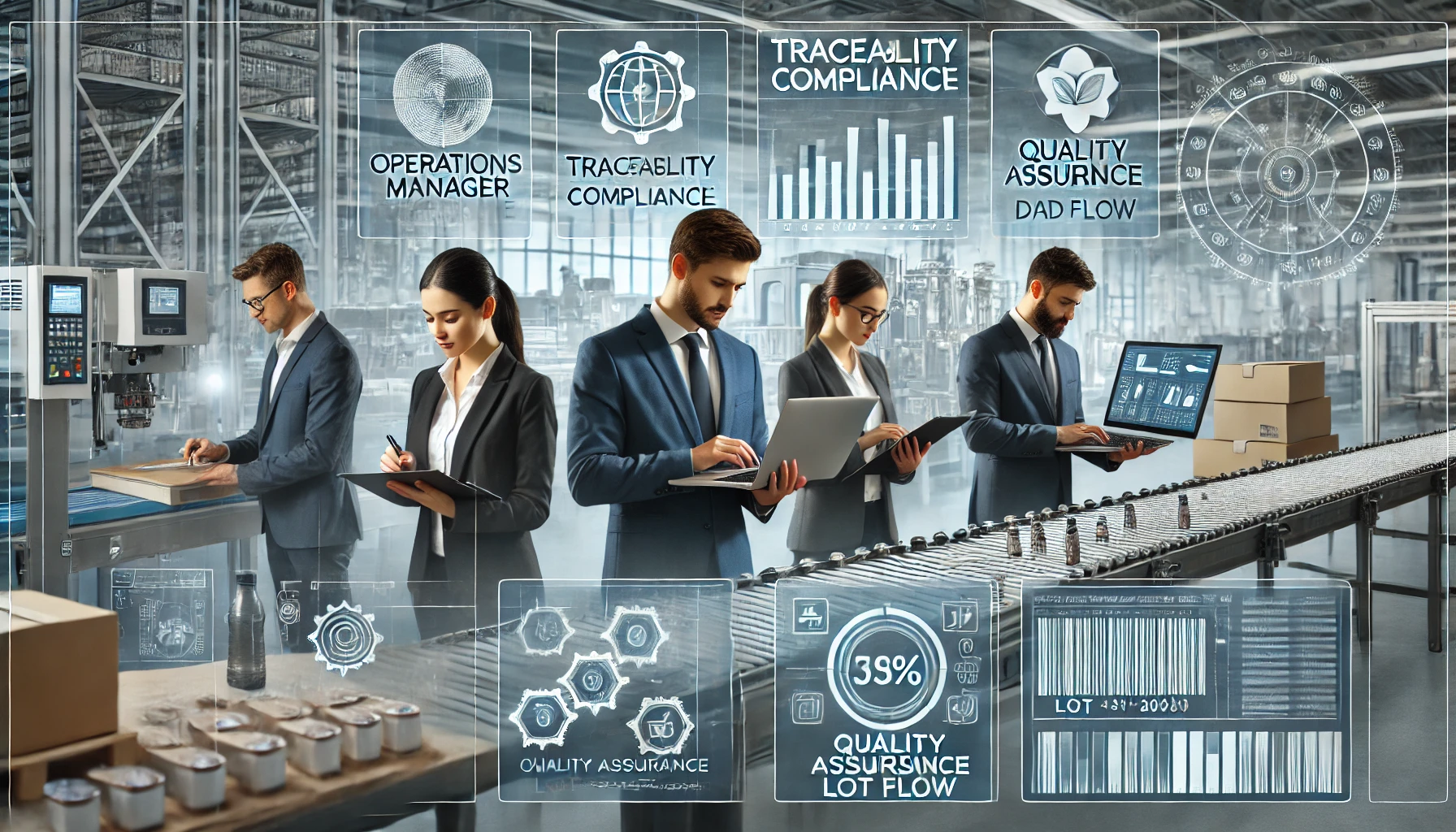
Learn how to prepare for FDA traceability inspections and why automated no-code solutions are essential for demonstrating compliance to inspectors.
Table of Contents
- Understanding FDA Traceability Inspections
- What FDA Inspectors Look For
- 1. Traceability Program Documentation
- 2. Traceability Records
- 3. Record Accessibility
- 4. Traceability Testing
- Before the Inspection: Preparation Checklist
- Documentation Readiness
- Record Systems
- Staff Preparation
- Facility Readiness
- During the Inspection: Best Practices
- 1. Designate a Point Person
- 2. Demonstrate Your System
- 3. Answer Questions Clearly
- 4. Document the Inspection
- 5. Address Issues Proactively
- Common Inspection Scenarios and How to Handle Them
- Scenario 1: Tracing a Specific Lot
- Scenario 2: Records Retrieval Test
- Scenario 3: Supplier Information Request
- Scenario 4: Lot Code Explanation
- After the Inspection: Follow-Up Actions
- 1. Review Inspection Findings
- 2. Develop Corrective Actions
- 3. Respond to FDA Communications
- 4. Upgrade to Automated Traceability Solutions
- 5. Avoid Custom Coding Pitfalls
- 6. Leverage Technology for Continuous Improvement
- 7. Conduct Internal Audits
- Need Help Preparing for FDA Inspections?
- Additional Resources
Understanding FDA Traceability Inspections
As the FDA’s Food Traceability Rule implementation progresses, businesses handling foods on the Food Traceability List (FTL) can expect increased regulatory oversight. FDA inspections will focus on verifying compliance with traceability requirements and evaluating the effectiveness of your traceability systems.
Being prepared for these inspections is essential to demonstrate compliance and avoid potential regulatory actions.
What FDA Inspectors Look For
During a traceability inspection, FDA officials typically evaluate:
1. Traceability Program Documentation
- Written traceability procedures
- Staff training records
- Lot coding system documentation
- Record maintenance protocols
2. Traceability Records
- Complete and accurate Key Data Elements (KDEs)
- Records for all Critical Tracking Events (CTEs)
- Proper maintenance of traceability lot codes
- Linkages between incoming and outgoing products
3. Record Accessibility
- Ability to provide records within 24 hours
- Sortable electronic formats
- Searchable by product, date, or lot code
- Completeness of historical records (2-year retention)
4. Traceability Testing
- Results of mock recalls or trace exercises
- Response time metrics
- Accuracy of trace-back and trace-forward
- Identification of process gaps or improvements
Before the Inspection: Preparation Checklist
To ensure you’re ready for an FDA traceability inspection, complete this preparation checklist:
Documentation Readiness
- Compile a traceability program manual
- Update SOPs for all Critical Tracking Events
- Organize training records for traceability staff
- Document your lot coding system methodology
- Prepare flow charts of your traceability process
Record Systems
- Ensure all required KDEs are being captured
- Verify records are maintained for at least 2 years
- Confirm records are in sortable electronic format
- Test your ability to retrieve records quickly
- Validate data accuracy across your systems
Staff Preparation
- Train key personnel on inspection protocols
- Designate traceability point persons
- Conduct mock interviews with staff
- Review common inspection questions
- Clarify roles during an actual inspection
Facility Readiness
- Organize a dedicated space for inspectors
- Prepare examples of traceability documentation
- Ensure access to electronic record systems
- Have product and ingredient lists available
- Compile supplier and customer contact information
During the Inspection: Best Practices
When FDA inspectors arrive, follow these best practices to facilitate a smooth inspection:
1. Designate a Point Person
- Assign a knowledgeable staff member to accompany inspectors
- Ensure this person understands traceability requirements
- Have backup personnel available if needed
2. Demonstrate Your System
- Show how your traceability system works
- Walk through a sample product trace
- Explain your lot coding methodology
- Demonstrate record retrieval capabilities
3. Answer Questions Clearly
- Provide direct, factual responses
- Avoid speculation or guessing
- If you don’t know an answer, say so and offer to find out
- Document questions that require follow-up
4. Document the Inspection
- Take notes on inspector comments and questions
- Record any requests for additional information
- Note any areas of concern raised by inspectors
- Document what records were reviewed
5. Address Issues Proactively
- If gaps are identified, acknowledge them
- Explain any corrective actions already in progress
- Provide timeframes for addressing new concerns
- Demonstrate commitment to compliance
Common Inspection Scenarios and How to Handle Them
Scenario 1: Tracing a Specific Lot
Inspector Request: “Show me how you would trace this specific lot of product through your facility.”
How to Respond:
- Retrieve the lot information from your system
- Demonstrate connections to incoming ingredients
- Show shipping records for the finished product
- Explain how the lot code maintains continuity
Scenario 2: Records Retrieval Test
Inspector Request: “I need to see all records related to this product received on this date.”
How to Respond:
- Use your electronic system to filter by date and product
- Show all associated KDEs for the receiving event
- Demonstrate links to subsequent processing or shipping events
- Provide the information within the expected timeframe
Scenario 3: Supplier Information Request
Inspector Request: “Show me the traceability information you received from your suppliers for this ingredient.”
How to Respond:
- Access supplier documentation in your system
- Show how supplier lot codes are recorded and maintained
- Demonstrate how you link supplier information to your internal records
- Explain any transformation or processing steps applied
Scenario 4: Lot Code Explanation
Inspector Request: “Explain your lot coding system and how it ensures traceability.”
How to Respond:
- Provide documentation of your lot coding methodology
- Explain each component of the lot code (date, line, batch, etc.)
- Show examples of how the code appears on products and records
- Demonstrate how the code enables precise tracing
After the Inspection: Follow-Up Actions
Once the inspection concludes, take these important follow-up steps:
1. Review Inspection Findings
- Carefully review any Form 483 observations (if issued)
- Understand the specific compliance concerns
- Clarify any points of confusion with the inspector
2. Develop Corrective Actions
- Create a detailed plan to address any identified issues
- Assign responsibilities for implementing changes
- Establish realistic timeframes for completion
- Document all corrective actions taken
3. Respond to FDA Communications
- Provide timely written responses to any FDA requests
- Detail your corrective action plans
- Include supporting documentation
- Maintain professional communication
4. Upgrade to Automated Traceability Solutions
- Replace manual processes with automated systems
- Implement no-code platforms rather than custom development
- Choose solutions with built-in FDA compliance validation
- Look for rapid implementation capabilities to address findings quickly
5. Avoid Custom Coding Pitfalls
- Custom-coded solutions often delay compliance remediation
- Regulatory changes require constant code revisions
- Testing and validation of custom code adds significant time
- Developer dependencies create business continuity risks
6. Leverage Technology for Continuous Improvement
- Implement automated data validation to prevent future findings
- Use real-time dashboards to monitor compliance metrics
- Deploy exception alerts to catch issues before inspectors do
- Adopt simulation tools to test process changes
7. Conduct Internal Audits
- Perform self-inspections using FDA criteria
- Test your improved traceability system
- Verify that corrective actions are effective
- Document all audit findings and resolutions
- Use automated audit tools to increase frequency and coverage
Need Help Preparing for FDA Inspections?
Preparing for FDA traceability inspections requires thorough understanding of regulatory requirements and effective implementation of compliant systems. Our team of food safety and regulatory experts can help you:
- Conduct pre-inspection readiness assessments
- Develop comprehensive traceability programs
- Train your staff on inspection protocols
- Implement effective record management systems
👉 Contact us today for inspection readiness support.