- Published at
Key Data Elements (KDEs) for FDA Traceability Compliance
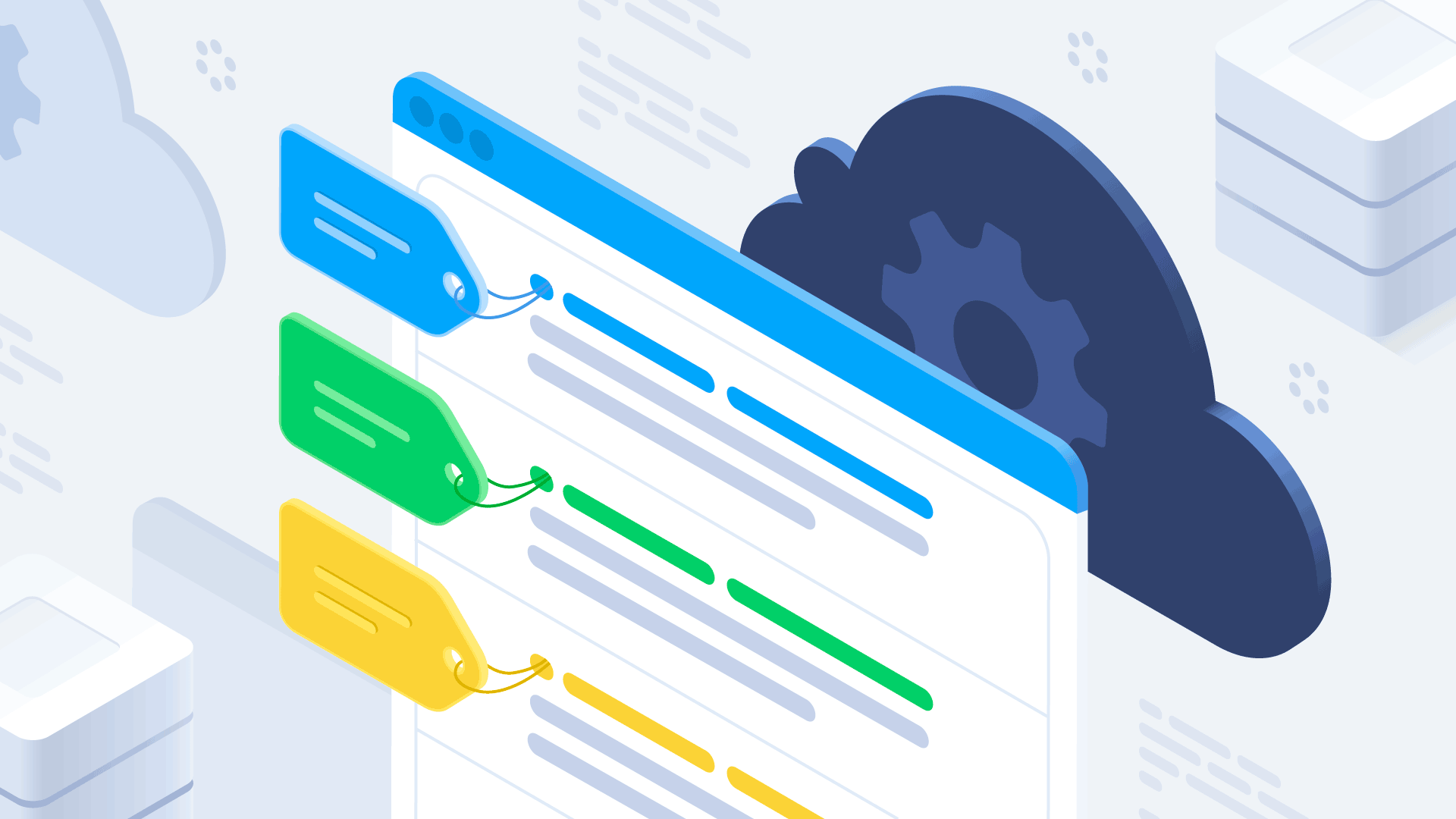
A detailed guide to the essential data points required for FDA traceability compliance and why no-code automation is critical for effective KDE management.
Table of Contents
- What Are Key Data Elements?
- Essential Key Data Elements for Traceability
- 1. Traceability Lot Code
- 2. Location Identifiers
- 3. Date and Time Information
- 4. Product Description
- 5. Quantity and Unit of Measure
- 6. Reference Records
- KDEs Required for Each Critical Tracking Event
- Growing KDEs
- Initial Packing KDEs
- Processing/Manufacturing KDEs
- Shipping KDEs
- Receiving KDEs
- Best Practices for KDE Collection and Management
- 1. Standardize Data Formats
- 2. Implement Data Validation
- 3. Minimize Manual Entry
- 4. Establish Data Hierarchies
- 5. Ensure Data Accessibility
- Common KDE Challenges and Solutions
- Challenge: Inconsistent Lot Code Formats
- Challenge: Missing Data from Suppliers
- Challenge: Managing Data Volume
- Challenge: Connecting KDEs Across Events
- Challenge: Maintaining Historical Records
- Technology Solutions for KDE Management
- 1. No-Code Traceability Platforms
- 2. The Dangers of Custom-Coded Solutions
- 3. Enterprise Resource Planning (ERP) Systems
- 4. Blockchain Solutions
- 5. Cloud-Based Data Management
- 6. Mobile Data Collection
- Need Help Managing Your KDEs?
- Additional Resources
What Are Key Data Elements?
Key Data Elements (KDEs) are the specific pieces of information that must be collected and maintained at each Critical Tracking Event (CTE) in your supply chain. They provide the essential data points needed to trace food products from their source to their destination.
Under the FDA’s Food Traceability Rule, businesses handling foods on the Food Traceability List must record these KDEs to create a complete traceability record that can be shared within 24 hours if requested by the FDA.
Essential Key Data Elements for Traceability
While specific KDEs vary by Critical Tracking Event, several core data elements appear consistently across the traceability continuum:
1. Traceability Lot Code
- A unique identifier assigned to a product lot or batch
- Must follow a consistent format that your company establishes
- Should be maintained throughout the supply chain
2. Location Identifiers
- Physical address of the location where the CTE occurs
- May include FDA registration numbers, DUNS numbers, or GLNs
- Both origin and destination locations for transfer events
3. Date and Time Information
- Date when the CTE occurred
- May include time stamps for high-risk products
- Date format should be consistent (e.g., YYYY-MM-DD)
4. Product Description
- Clear identification of the food item
- May include variety, brand name, or commodity
- Should match commercial documentation
5. Quantity and Unit of Measure
- Amount of product involved in the CTE
- Consistent units (e.g., cases, pounds, kilograms)
- Should reconcile across shipping and receiving records
6. Reference Records
- Links to related business documents
- May include purchase orders, BOLs, invoices
- Creates connections between traceability data points
KDEs Required for Each Critical Tracking Event
Each type of Critical Tracking Event requires specific Key Data Elements:
Growing KDEs
- Location description (field or growing area)
- Traceability lot code
- Location identifier (coordinates or address)
- Commodity and variety
- Date of harvest
- Quantity harvested and unit of measure
Initial Packing KDEs
- Location where packing occurred
- Traceability lot code assignment
- Date of packing
- Commodity and variety
- Quantity packed and unit of measure
- Reference to growing information
Processing/Manufacturing KDEs
- Location where processing occurred
- Traceability lot code assignment
- Date of processing/manufacturing
- Description of the food produced
- Quantity produced and unit of measure
- References to incoming ingredients and their lot codes
- Processing steps applied (optional but recommended)
Shipping KDEs
- Location shipping from
- Location shipping to
- Date of shipping
- Traceability lot code(s) being shipped
- Description of food being shipped
- Quantity shipped and unit of measure
- Reference to transporter information
- Expected arrival date (optional but recommended)
Receiving KDEs
- Location receiving at
- Location received from
- Date of receipt
- Traceability lot code(s) received
- Description of food received
- Quantity received and unit of measure
- Receipt status (accepted/rejected)
Best Practices for KDE Collection and Management
To ensure your KDE records meet FDA requirements and support effective traceability:
1. Standardize Data Formats
- Use consistent date formats (YYYY-MM-DD recommended)
- Standardize product descriptions across your organization
- Develop a uniform lot coding system
2. Implement Data Validation
- Create systems that verify data completeness
- Use dropdown menus instead of free text when possible
- Implement automatic checks for required fields
3. Minimize Manual Entry
- Use barcode scanning or automated data capture
- Implement electronic record systems
- Reduce opportunities for human error
4. Establish Data Hierarchies
- Create clear relationships between products, lots, and shipments
- Maintain parent-child relationships for ingredients and finished goods
- Document transformation ratios for processing events
5. Ensure Data Accessibility
- Store KDEs in sortable, searchable formats
- Maintain records that can be provided within 24 hours
- Create systems for rapid data retrieval during investigations
Common KDE Challenges and Solutions
Challenge: Inconsistent Lot Code Formats
Solution: Develop a standardized lot coding system that includes date, production line, and batch information in a consistent format.
Challenge: Missing Data from Suppliers
Solution: Create supplier agreements that require all necessary KDEs and provide templates for data submission.
Challenge: Managing Data Volume
Solution: Implement a dedicated traceability or ERP system that can handle large volumes of data while maintaining accessibility.
Challenge: Connecting KDEs Across Events
Solution: Use reference numbers or identifiers that link related events, such as connecting a receiving event to its corresponding shipping event.
Challenge: Maintaining Historical Records
Solution: Implement a data retention policy that preserves traceability records for at least 2 years while ensuring they remain accessible.
Technology Solutions for KDE Management
The right technology approach is critical for effective KDE management. Here’s what you need to know:
1. No-Code Traceability Platforms
- Ready out-of-the-box with FDA compliance built in
- Configurable without coding to match your specific processes
- Regular updates to stay current with regulatory changes
- Rapid implementation compared to custom development
2. The Dangers of Custom-Coded Solutions
- Development delays often jeopardize compliance deadlines
- Maintenance burden grows with each regulatory update
- Knowledge dependency on specific developers or vendors
- Integration challenges with existing systems
- Testing requirements increase with each code change
3. Enterprise Resource Planning (ERP) Systems
- Integrates traceability with other business functions
- Can automate KDE collection during normal operations
- Provides reporting capabilities for compliance
- Consider ERP add-ons rather than custom development
4. Blockchain Solutions
- Creates immutable records of traceability data
- Enables secure sharing across supply chain partners
- Provides transparency and verification
- Look for no-code blockchain platforms with FDA templates
5. Cloud-Based Data Management
- Allows access from multiple locations
- Simplifies data sharing during investigations
- Provides backup and redundancy for critical records
- Eliminates on-premise infrastructure management
6. Mobile Data Collection
- Smartphone apps for capturing KDEs at the point of action
- Offline capabilities for areas with poor connectivity
- Built-in validation to prevent incomplete records
- Photo documentation capabilities for visual verification
Need Help Managing Your KDEs?
Properly collecting and maintaining Key Data Elements is essential for FDA compliance and effective traceability. Our team can help you develop systems and procedures tailored to your specific operations.
👉 Contact us today for a consultation or system assessment.